摘要: 本文深入探討了大包回轉臺
液壓滑環(huán)在冶金連鑄機械中的關鍵應用。首先闡述冶金連鑄工藝的基本流程以及大包回轉臺在其中的核心地位,隨后詳細剖析
YH型液壓滑環(huán)的結構、工作原理與技術特點,分析其在提升連鑄生產效率、保障設備穩(wěn)定運行以及優(yōu)化連鑄產品質量等方面的顯著優(yōu)勢,并結合實際案例展示其應用成效,最后對其未來發(fā)展趨勢進行展望,旨在全面呈現(xiàn)該液壓滑環(huán)在冶金連鑄領域的重要性與廣闊前景。
在現(xiàn)代冶金工業(yè)中,連鑄技術是鋼鐵生產的關鍵環(huán)節(jié),它將煉鋼爐中熔煉的液態(tài)鋼水連續(xù)鑄造成固態(tài)鑄坯,極大地提高了生產效率和鋼材質量。大包回轉臺作為連鑄生產線的重要設備,承擔著將鋼水包中的鋼水精準地分配到各個中間包的重任。而
大包回轉臺液壓滑環(huán)則是確保大包回轉臺高效、穩(wěn)定運行的關鍵部件,其性能的優(yōu)劣直接影響到整個連鑄生產過程的連續(xù)性、穩(wěn)定性和產品質量。
冶金連鑄工藝主要包含鋼水準備、澆鑄、凝固成型和鑄坯處理等步驟。煉鋼爐煉制出合格的鋼水后,倒入鋼水包,由天車吊運至連鑄車間的大包回轉臺上方。鋼水通過大包回轉臺的旋轉和升降動作,經(jīng)水口流入中間包,中間包起到緩沖、穩(wěn)流和分配鋼水的作用,使鋼水均勻地流入結晶器。在結晶器中,鋼水在水冷銅壁的冷卻作用下,開始凝固形成坯殼,隨著拉坯機的牽引,鑄坯逐漸從結晶器中拉出,并在二次冷卻區(qū)進一步冷卻和凝固,最終通過切割設備切割成定尺的鑄坯,完成連鑄生產過程。
大包回轉臺位于連鑄生產線的澆鑄平臺中心位置,它需要實現(xiàn)鋼水包的快速更換、精確對中以及穩(wěn)定澆鑄等功能。在連鑄過程中,大包回轉臺要頻繁地進行旋轉、升降和微調等操作,以確保鋼水能夠準確無誤地流入中間包,并且要適應不同鋼種、不同澆鑄速度和不同鋼水包容量的要求。例如,在更換鋼水包時,大包回轉臺需迅速將空包轉出,同時將滿包轉入澆鑄位置,并保證水口與中間包的對接精度在毫米級范圍內,以防止鋼水溢出或澆鑄中斷等事故的發(fā)生。因此,大包回轉臺必須具備高可靠性、高精度和高穩(wěn)定性的運行特性。
大包回轉臺液壓滑環(huán)通常由定子、轉子、液壓通道、密封裝置、電氣信號傳輸部件等部分組成。定子部分固定安裝在連鑄機的基礎框架上,它包含了與外部液壓系統(tǒng)和控制系統(tǒng)相連的接口,是液壓油和電氣信號的輸入輸出端。轉子部分則與大包回轉臺的旋轉軸剛性連接,隨回轉臺一起轉動。液壓通道貫穿定子和轉子,為液壓油在靜止與旋轉部件之間的傳輸提供路徑,其內部通道設計經(jīng)過優(yōu)化,以減小液壓油的流動阻力并確保流量的穩(wěn)定。密封裝置采用了特殊的密封材料和結構,如高性能的橡膠密封件和機械密封組合,有效防止液壓油泄漏和外界雜質進入滑環(huán)內部。電氣信號傳輸部件則負責在定子和轉子之間傳遞諸如位置傳感器信號、控制信號等電氣信息,保證回轉臺與控制系統(tǒng)之間的實時通信。
當大包回轉臺進行旋轉或升降動作時,轉子相對于定子發(fā)生相對運動。外部液壓系統(tǒng)提供的液壓油通過定子的液壓入口進入液壓滑環(huán)的液壓通道,在轉子的帶動下,液壓油沿著通道流向安裝在大包回轉臺上的各個液壓執(zhí)行元件,如液壓缸,為回轉臺的動作提供動力支持。同時,回轉臺上的傳感器采集到的位置、壓力等信號通過電氣信號傳輸部件傳遞到定子,再由定子傳輸至連鑄生產線的控制系統(tǒng)??刂葡到y(tǒng)根據(jù)這些信號對大包回轉臺的運行進行精確控制,如調整回轉臺的旋轉速度、停止位置以及液壓執(zhí)行元件的動作順序等。在整個過程中,液壓滑環(huán)通過巧妙的結構設計,實現(xiàn)了液壓動力和電氣信號在旋轉與靜止部件之間的連續(xù)、穩(wěn)定傳輸,確保了大包回轉臺的靈活、可靠運行。
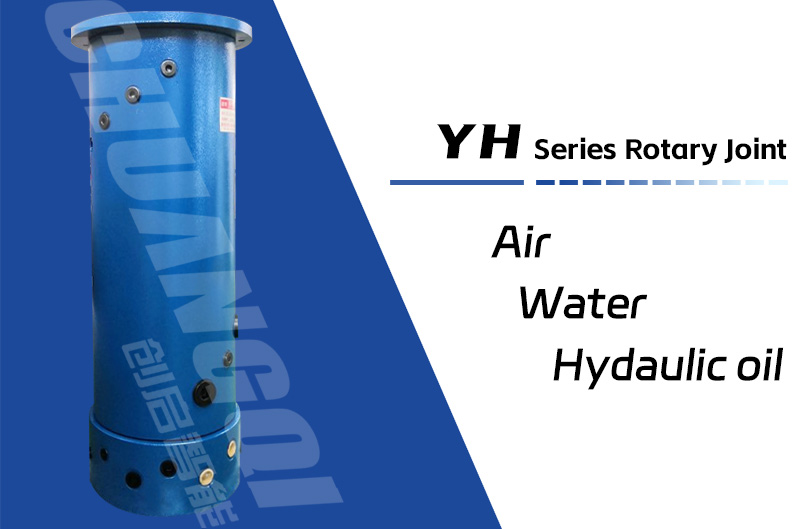
卓越的密封性能
大包回轉臺液壓滑環(huán)采用了先進的密封技術,其密封結構能夠承受高溫、高壓以及惡劣的工作環(huán)境。多重密封設計有效防止了液壓油的泄漏,確保了液壓系統(tǒng)的壓力穩(wěn)定,避免了因泄漏導致的設備故障和安全事故。例如,在長時間連續(xù)澆鑄過程中,密封裝置能夠保持良好的密封效果,使液壓滑環(huán)的泄漏率極低,保證了大包回轉臺的穩(wěn)定運行。
可靠的電氣信號傳輸
電氣信號傳輸部件采用了抗干擾能力強的設計,能夠在強電磁干擾環(huán)境下準確地傳輸各種電氣信號。無論是位置傳感器的微弱信號還是控制信號的高頻信號,都能穩(wěn)定、可靠地在定子和轉子之間傳遞,為大包回轉臺的精確控制提供了堅實的保障。
優(yōu)化的液壓通道設計
液壓滑環(huán)內部的液壓通道經(jīng)過精心設計,具有較低的流阻系數(shù)。這使得液壓油在傳輸過程中能量損失較小,能夠以較高的效率將液壓動力傳遞到各個液壓執(zhí)行元件。與傳統(tǒng)的液壓管路連接方式相比,可減少液壓泵的輸出功率,從而實現(xiàn)節(jié)能降耗。據(jù)實際應用數(shù)據(jù)顯示,采用大包回轉臺液壓滑環(huán)后,液壓系統(tǒng)的能耗可降低約 10% - 15%。
快速響應特性
由于液壓滑環(huán)的結構緊湊,液壓油的傳輸路徑短,使得液壓執(zhí)行元件能夠快速響應控制系統(tǒng)的指令。在大包回轉臺的旋轉、升降等動作中,能夠實現(xiàn)快速、精準的控制,提高了連鑄生產的效率。例如,在更換鋼水包時,大包回轉臺能夠迅速完成動作轉換,減少了澆鑄中斷時間。
廣泛的工況適應性
大包回轉臺液壓滑環(huán)能夠適應不同型號、不同規(guī)格的大包回轉臺以及各種復雜的連鑄工藝要求。無論是高溫鋼水澆鑄還是低溫特種鋼連鑄,它都能穩(wěn)定工作,并且能夠與不同品牌、不同類型的液壓系統(tǒng)和控制系統(tǒng)兼容,為冶金企業(yè)的設備選型和升級改造提供了便利。
便捷的維護保養(yǎng)
其模塊化的設計結構使得維護保養(yǎng)工作變得簡單易行。當液壓滑環(huán)出現(xiàn)故障時,可以快速更換故障模塊,而無需對整個設備進行大規(guī)模拆解和維修。同時,其密封件和易損部件的更換也較為方便,降低了設備的維護成本和停機時間。
某鋼鐵企業(yè)的連鑄生產線在升級改造前,大包回轉臺采用傳統(tǒng)的液壓管路連接方式,經(jīng)常出現(xiàn)液壓油泄漏、信號傳輸不穩(wěn)定等問題,導致大包回轉臺的運行故障率較高,每月平均停機維修時間長達 12 小時左右,嚴重影響了連鑄生產的連續(xù)性和效率。同時,由于液壓系統(tǒng)的能耗較高,企業(yè)的生產成本也居高不下。
在對連鑄生產線進行技術改造時,該企業(yè)采用了大包回轉臺液壓滑環(huán)。改造后,大包回轉臺的運行穩(wěn)定性得到了顯著提升,液壓油泄漏問題得到有效解決,信號傳輸準確可靠。設備故障率大幅降低,每月平均停機維修時間縮短至 2 小時以內,連鑄生產效率提高了約 15%。在能耗方面,液壓系統(tǒng)的能耗降低了約 12%,每年為企業(yè)節(jié)省了大量的能源成本。此外,由于液壓滑環(huán)的維護便利性,設備的維護保養(yǎng)工作變得更加高效,進一步降低了企業(yè)的運營成本。
隨著冶金工業(yè)的不斷發(fā)展和技術創(chuàng)新,大包回轉臺液壓滑環(huán)也將朝著更高性能、智能化和綠色環(huán)保的方向發(fā)展。
高性能材料的應用
未來有望研發(fā)和應用更高性能的密封材料、耐磨材料和導電材料,進一步提高液壓滑環(huán)的密封性能、使用壽命和信號傳輸質量。例如,新型的納米復合材料可能會應用于密封裝置,使其在更極端的工況下仍能保持良好的密封效果。
智能化技術集成
隨著工業(yè)互聯(lián)網(wǎng)和人工智能技術的發(fā)展,大包回轉臺液壓滑環(huán)將集成更多的智能化功能。如內置傳感器實現(xiàn)對自身運行狀態(tài)的實時監(jiān)測和故障預警,通過物聯(lián)網(wǎng)技術與連鑄生產線的控制系統(tǒng)進行深度融合,實現(xiàn)遠程診斷和智能控制,提高設備的運維效率和生產管理水平。
綠色環(huán)保設計
在環(huán)保要求日益嚴格的背景下,液壓滑環(huán)的設計將更加注重節(jié)能減排和資源循環(huán)利用。例如,優(yōu)化液壓系統(tǒng)的設計,降低液壓油的用量和泄漏風險,采用可回收材料制造滑環(huán)部件等,以減少對環(huán)境的影響。
綜上所述,大包回轉臺液壓滑環(huán)在冶金連鑄機械中具有極為重要的應用價值。它通過其獨特的結構、先進的工作原理和顯著的技術優(yōu)勢,為大包回轉臺的穩(wěn)定運行、連鑄生產效率的提高和產品質量的保障提供了有力支持。隨著未來技術的不斷進步,其必將在冶金連鑄領域發(fā)揮更加重要的作用,推動冶金工業(yè)的持續(xù)發(fā)展。